As the world shifts towards sustainable transportation, electric vehicles (EVs) are leading the charge. World EV Day, celebrated on September 9, highlights the importance of electric mobility and the innovations driving it forward. One such innovation is the use of laser cutting, laser marking, and laser welding in EV manufacturing, offering unparalleled precision and efficiency.
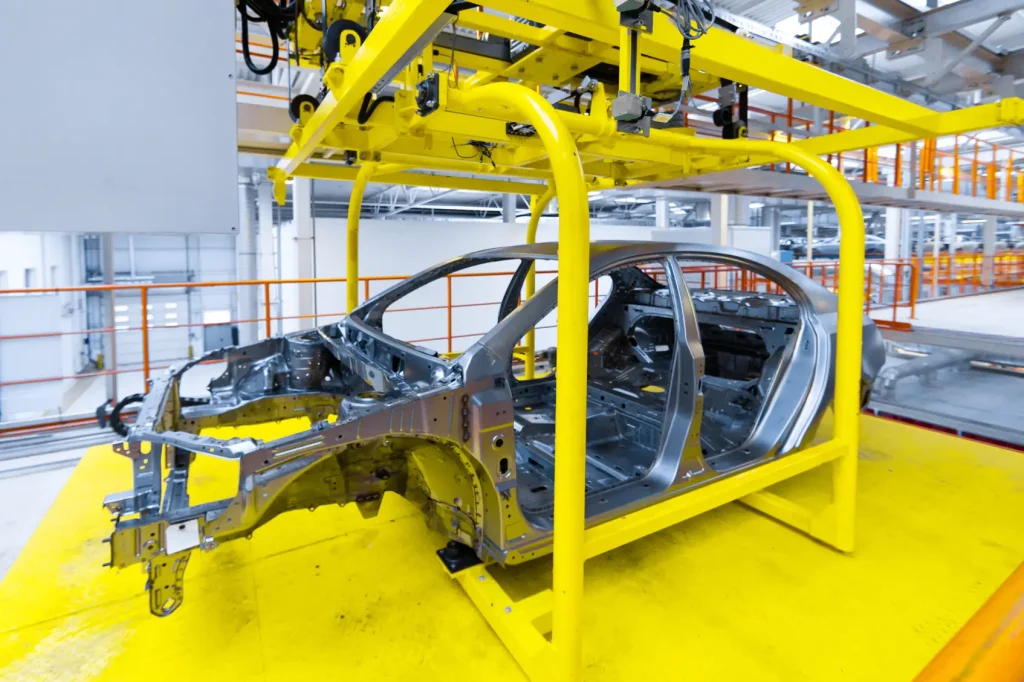
SLTL Group, a global leader in laser solutions, is playing a key role in this transition by providing advanced fiber laser cutting machines and laser welding solutions that meet the evolving needs of the electric vehicle industry. In this blog, we’ll explore the significance of SLTL’s laser systems in manufacturing key EV components, from sensors to inverters, and how laser cutting, laser marking, and laser welding are shaping the future of electric vehicles.
1. Fiber Laser Cutting and Laser Welding in EV Manufacturing
SLTL’s fiber laser cutting technology plays a vital role in producing electric vehicle components. The precision and flexibility of fiber laser cutting make it ideal for producing complex shapes and designs used in EV batteries, motors, and structural parts. Additionally, laser welding provides strong, durable joints for critical components like battery casings and motor housings.

Whether it’s the precise laser cutting of metal parts, or the durable, damage-free markings applied to components, SLTL’s fiber laser cutting, laser marking, and laser welding technologies ensure that manufacturers can produce electric vehicles with the highest level of quality and efficiency.
2. Laser Marking for Sensors and Cameras
In electric vehicles, sensors and cameras are vital for advanced driver assistance systems (ADAS) and autonomous driving. Ensuring these components are easily identifiable and traceable is crucial, and laser marking offers the perfect solution.
Sonar Sensors: Installed in bumpers, sonar sensors detect obstacles while parking. Using laser marking, each sensor’s casing is permanently labeled, allowing for traceability across a variety of colored and coated surfaces.
Front and Rear Cameras: EVs are equipped with multiple cameras for parking assist and other ADAS functions. Laser marking is applied to camera lenses and e-coated parts, ensuring clear identification without damaging the protective coatings that prevent rust.
3. Battery Components and Laser Marking
The battery is the most critical component of an electric vehicle, especially the widely used lithium-ion batteries. Ensuring traceability and quality in battery production is paramount, and laser marking plays an essential role.
2D Code and Serial Number Marking: SLTL’s laser marking technology is used to apply 2D codes and serial numbers on battery covers, aiding in easy identification during assembly and future maintenance.
Battery Surface Roughening: Beyond marking, SLTL’s fiber laser cutting machines also roughen battery surfaces, improving bonding strength during assembly. This process is critical for ensuring the reliability and durability of EV batteries.
Electrode Marking: With the increasing complexity of EV batteries, the precise traceability of individual components, such as electrodes, is becoming more important. Laser marking allows manufacturers to mark each electrode for detailed tracking.
4. Laser Marking and Cutting for Inverters
Inverters convert the DC electricity stored in the EV’s battery to AC power for the electric motor, making them critical to vehicle performance. Laser cutting, laser marking, and laser welding are essential in the production and identification of inverter components.
PCB Marking: Inverters contain printed circuit boards (PCBs) that require precise laser marking. SLTL’s laser marking technology ensures that 2D codes are applied without damaging the glass epoxy substrate, protecting the intricate circuits.
Cooling Device Marking: Inverters generate significant heat during operation. Using laser marking, cooling devices are permanently labeled with specifications, aiding in traceability and ensuring proper assembly.
Aluminum Cast Parts: Inverter cases are typically made from aluminum castings. SLTL’s fiber laser cutting and laser marking machines provide permanent identification of cast parts without causing any damage, allowing for easy quality control.
Conclusion
As we celebrate World EV Day, it’s essential to recognize the technologies driving the electric vehicle revolution. SLTL’s fiber laser cutting, laser marking, and laser welding solutions are crucial in manufacturing key EV components, from batteries to sensors and inverters. These technologies offer precision, durability, and efficiency, helping automakers produce electric vehicles that are safer, more reliable, and environmentally friendly.
SLTL’s commitment to innovation ensures that the electric vehicle industry continues to thrive, with fiber laser cutting, laser marking, and laser welding at the heart of this transformation. As the demand for electric vehicles grows, so too will the need for advanced manufacturing solutions like those provided by SLTL. This World EV Day 2024, let’s celebrate the role of laser solutions in shaping a sustainable future for transportation.